Extrusion Plastometer | MFI Tester China Manufacturer
Melt Flow Indexer is also referred to as the extrusion plastometer or MFI instrument. It is intended to determine the melt flow rate of various molten thermoplastic materials extruded from the die with a specified length and bore diameter under specified conditions of temperature and load. The melt flow index tester is extensively applicable to materials with high melting temperatures, including polycarbonate, poly sulfoxide, fluoroplastics, nylon, etc., and plastics with low melting temperatures like PE, PS, PP, ABS, POM, PC, etc.
The determination of melt flow index (MFI) is divided into two methods of measuring melt mass-flow rate(MFR) and melt volume-rate(MVR). MFR is expressed by the gram per 10 minutes based on the mass of the molten material extruded from the die over the given period. MVR is expressed by the cubic centimetre per 10 minutes based on the volume of material extruded from the die over the specified period.
AmadeTech melt flow indexer features a vertical cylinder inside the top half made of wear and corrosion-resistant material. A heater surrounding the cylinder provides and maintains the required temperature for testing, and a temperature sensor is available to monitor the temperature inside the cylinder hole. A die with a bore is contained at the lower end of the cylinder hole. We equip the machine with a removable piston scribed two thin annular reference marks 30 mm apart on the stem, ensuring the distance between the lower edge of the piston head and the top of the die is 20 mm when the upper mark coincides with the top of the cylinder. You need to manually insert the piston into the heated cylinder and add the combined weights to give the material a specified load to allow the extrudate to flow out of the bore of the die.
AmadeTech can provide flexible equipment solutions. Our regular models of the melt flow index testers are capable of determining both the melt mass-flow rate (MFR) and the melt volume-flow rate (MVR). If the MVR measurement is not required during your test, A model that can only do MFR measurement is also available from AmadeTech to help you save equipment purchase costs. MFR measurement can be performed by either manual cut-off or automatically timed operation.
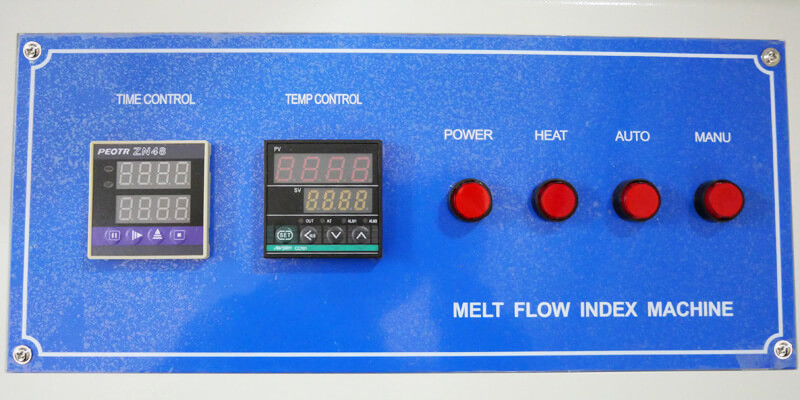
Push-button control panel
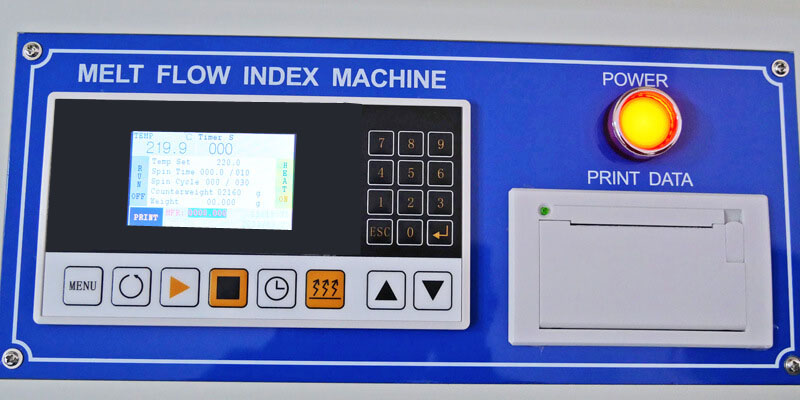
Key-type control panel
In addition, AmadeTech melt flow indexer’s control panel ranges from a traditional push-button operation panel with LED digital displays to a new key-type one with an LCD and thermal printer. You can select the corresponding model according to your preference.
If you are interested in more plastics testing instruments from AmadeTech, please click HERE.
Model | AT-P6003 |
Supported test methods | MFR & MVR |
Temperature control | RT~300°C (RT~400°C & RT~500℃ are optional)
Temperature fluctuation: ± 0.5℃ Temperature uniformity: ± 1℃ Temperature display resolution: 0.1℃ Sample preheat time: 4 minutes or user-defined |
Standard die dimensions | Φ2.095 ± 0.005 mm
Length: 8.000 mm ± 0.025 mm |
Cylinder dimensions | Internal diameter: 9.550 mm ± 0.025 mm
Length: 152 mm ± 0.1mm Hardness not less than 500 (HV5~HV100) |
Piston dimensions | Head length: 6.350 mm ± 0.100 mm
Head diameter: 9.474 mm ± 0.007 mm |
Weight precision | ± 0.5% |
Test results | Automatically calculate results and support printing |
Material cut-off methods for MFR | Manual / automatic |
Position displacement detection for MVR | Travel length: 30 mm
Control precision: ± 0.1 mm |
Material cut-off time-interval | 0 ~ 999 s |
Number of cut-off cycles | 0 ~ 999 s |
Time display resolution | 0.1 s |
Test Load | 8 grades in total (7 pcs of weights & a piston) |
Power supply | AC 220V ± 10%, 50 Hz or / AC 110V ± 10% 60 Hz |
- ISO 1133 Plastics determination of the melt mass flow rate (MFR) and melt volume flow rate (MVR) of thermoplastics.
- GBT 3682-2000 Determination of the melt mass-flow rate (MFR)and the melt volume-flow rate(MVR)of thermoplastics.
- JIS K7210 Plastics Determination of the melt mass-flow rate (MFR) and melt volume-flow rate (MVR) of thermoplastics.Part 1: Standard method.
The specimen in a specified quantity is placed in the barrel of the melt flow tester and heated to reach a molten state under the specified temperature condition. The melt is extruded from a die of a specified length and diameter under a prescribed load. For MFR, timed segments of the extrudate are weighed, and the extrudate rate is calculated in g/10m. For MVR, the time required for the piston to move a specified distance is measured to generate a result in cm3/10m.
AmadeTech MFI Tester Features
- Made of hard material in line with standard requirements.
- Supports MFR & MVR measurements (for regular models).
- Fitted with an LCD to assist in parameter setting and show the real-time running state (for regular models).
- Has flexible temperature options, and the maximum is as high as 500°C.
- A dual temperature control system allows more accurate temperature control and higher heating efficiency.
- Equipped with a spatula to manually & automatically cut off the extrudate.
- Provided with an encoder to record the piston displacement automatically, the system can measure the times taken.
- Multiple weights in different levels are provided to enable different combined loads.
- Able to calculate test results automatically, and printing on-site is available.
FAQs
Leave Your Message Here
Please feel free to contact us for more details on the product, price, lead time, payment terms, shipment methods, etc. Amadetech sales specialists will respond within one working day.