Melt flow index (MFI) is a measure of how easily a thermoplastic material can flow under a specified pressure and temperature. It is an indicator of the viscosity and molecular weight of the polymer. MFI is widely used in the plastics industry to assess the processability and quality of different materials.
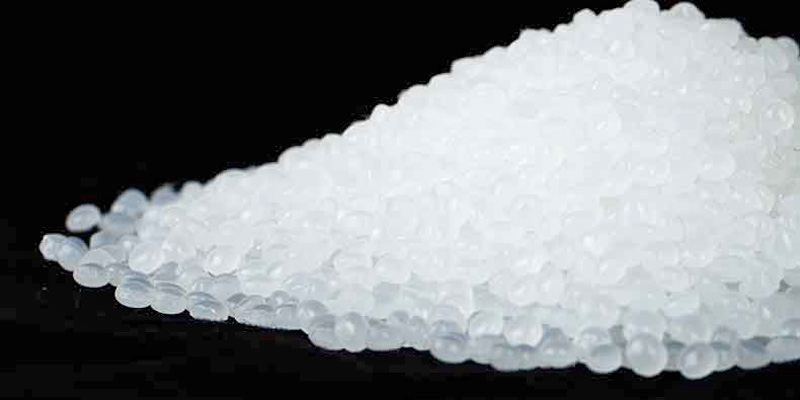
Why Is MFI Important?
MFI is essential for several reasons.
First, it affects the molding and extrusion behaviour of the plastic. A higher MFI means a lower viscosity and a faster flow rate, which can improve the filling and dimensional stability of the molded or extruded part. However, a too-high MFI can also cause problems such as sagging, flashing, or poor mechanical properties.
Second, MFI reflects the polymer’s molecular weight and molecular weight distribution. A lower MFI means a higher molecular weight and a higher degree of polymerization, which can enhance the plastic’s strength, toughness, and heat resistance. However, a too-low MFI can also cause difficulties in processing, such as high shear stress, degradation, or poor dispersion of additives.
Third, MFI can be used as a quality control tool to monitor the consistency and reliability of the plastic. MFI can be influenced by various factors during the production and storage of plastic. For example, temperature, pressure, residence time, moisture content, additives, and contaminants can all affect the MFI of the material.
How to Measure MFI?
MFI is measured by using a testing machine called a melt flow indexer or extrusion plastometer. The device has a heated barrel with a die at one end and a piston to act on the sample material. A known mass of plastic is placed in the barrel and heated to a specified temperature. Then, a constant load is applied to the piston to force the molten plastic through the die. The amount of plastic that flows out of the die in 10 minutes is recorded as the MFI value. The test conditions (temperature, load, and die diameter) vary depending on the type and grade of the plastic.
MFI can be obtained by measuring MFR or MVR. The most commonly used standards are ISO 1133 and ASTM D1238. The MFR is usually expressed in grams per 10 minutes (g/10 min), and the MVR is usually expressed in cubic centimetres per 10 minutes (cm3/10 min). The higher the MFI value, the lower the viscosity and molecular weight of the polymer.
What Are Some Applications of MFI?
MFI is used for various applications in the plastics industry. Some examples are:
- Material selection: MFI can help to choose the most suitable material for a specific application based on its processability and performance requirements.
- Material comparison: MFI can help to compare different materials or grades of the same material based on their viscosity and molecular weight characteristics.
- Material modification: MFI can help to evaluate the effect of additives, fillers, reinforcements, or blending on the properties of the material.
- Material identification: MFI can help to determine the molecular weight and molecular weight distribution of the polymer by using empirical or theoretical correlations.
- Material inspection: MFI can help to check the quality and consistency of the material by detecting any changes or variations in its viscosity and molecular weight.
What Are the Limitations of MFI?
Measuring MFI is a simple, fast, and inexpensive test method that can provide useful information about the flow behaviour and molecular weight distribution of thermoplastic materials. Although MFI has a number of advantages, however, MFI also has some limitations and drawbacks that should be considered.
MFI is not a direct measure of viscosity or molecular weight but rather an empirical value that depends on the test conditions. Therefore, MFI values are only comparable for materials tested under the same conditions. Moreover, MFI does not account for other factors that affect the flow behaviour of thermoplastics, such as shear rate, shear stress, shear history, temperature gradient, pressure drop, or rheological properties (such as shear thinning or viscoelasticity). Therefore, MFI may not accurately predict the actual flow behaviour of thermoplastics in complex molding processes or under varying operating conditions.
Conclusion
MFI is an important parameter that characterizes the flow behaviour and molecular weight of thermoplastic materials. It plays an active role in the selection, comparison and identification of product raw materials, the optimization control of production technology, and the quality control and consistency of products. But just like a coin has heads and tails, MFI also has its own limitations that we cannot ignore. Only by using it reasonably can it better assist our production and life.
If you have MFI testing needs, don’t hesitate to get in touch with AmadeTech. We can provide you with the corresponding MFI equipment. Our machines are designed and produced according to the ISO 1133 standard. One piece of equipment can be compatible with MFR and MRV tests and has very high-cost performance. According to the material characteristics, you are available to select different temperature upper limits for the machine ranging from 300°C to 500°C.
If you have any questions about testing, please let us know.