In the fast-paced world of manufacturing and packaging, ensuring the quality and safety of products is of utmost importance. Whether it is the food and beverage sector, pharmaceuticals, or electronics, packaging plays a crucial role in protecting products from external factors that can compromise their quality. One popular factor we should prevent is the presence of leaks, which can lead to spoilage, contamination, or even safety hazards. To address this concern, an innovative testing solution has emerged – the vacuum leak tester.
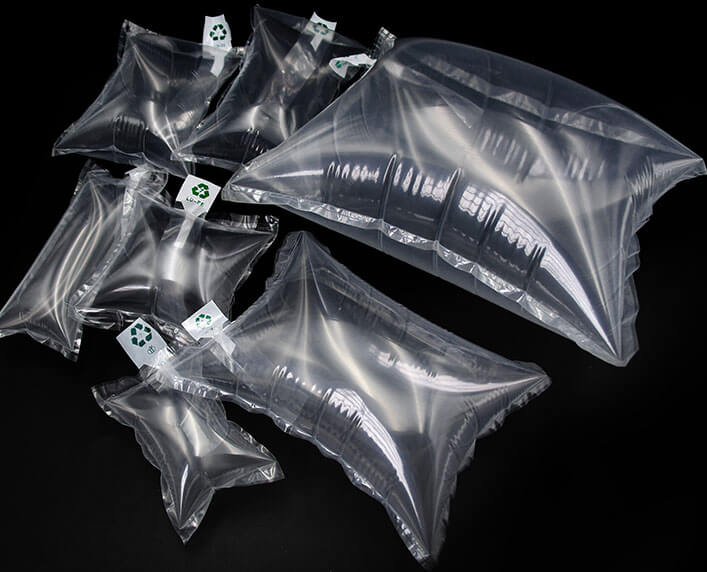
In this post, we will delve into the concept of vacuum leak testing, vacuum leak tester, its working principle, and the benefits it offers to businesses, and guide you on how to select a vacuum leak tester.
Understanding Vacuum Leak Testing for packaging
Vacuum leak testing is a non-destructive method used to identify leaks in sealed packages or containers. It involves submerging the packaging in the water and subjecting it to a negative pressure, determining if any leaks are present by observing whether progressive bubble emission occurs.
This method is highly effective in identifying even the smallest leaks that may compromise the integrity of the packaging. By detecting leaks early on, manufacturers can prevent product spoilage, maintain product quality, and ensure customer satisfaction.
The Importance of Vacuum Leak Testing in Packaging
- Product Quality Assurance
Vacuum leak testing plays a crucial role in ensuring the quality of packaged products. Leaks in packaging can lead to contamination, spoilage, and reduced shelf life. By utilizing a vacuum leak tester, manufacturers can identify and rectify any leaks before the products reach the market. This not only enhances the overall quality of the products but also safeguards the reputation of the brand.
- Consumer Safety
In addition to product quality, vacuum leak testing is vital for consumer safety. Certain products, such as food, pharmaceuticals, and chemicals, require an airtight seal to prevent contamination and maintain their efficacy. Any leaks in the packaging can compromise the safety of consumers, leading to potential health risks. By implementing vacuum leak testing, manufacturers can ensure that their products are safe for consumption or use.
- Cost Reduction
Detecting and addressing leaks early on can significantly reduce costs for manufacturers. Product recalls, returns, and customer complaints due to packaging failures can be costly and damaging to a company’s bottom line. By investing in a vacuum leak tester, manufacturers can identify and resolve leaks before the products are distributed, saving both time and money.
What Is a Vacuum Leak Tester for Packaging?
A vacuum leak tester for packaging is a specialized apparatus used in the packaging industry to conduct vacuum leak testing to check the integrity and quality of sealed packages. It is designed to detect any leaks or defects in the packaging, ensuring that the contents remain sealed and protected during storage, transportation, and handling.
The vacuum leak tester is especially suitable for flexible packaging with a handspace gas. It varies in different types and sizes to suit a wide variety of packages.
What Is the Woking Principle of the Vacuum Leak Tester for Packaging?
The vacuum leak tester features a transparent sealed container to provide a controlled vacuum environment. The sample packaging is required to be submerged in the water filled in this container. The negative pressure is gradually applied to the inside of the container until a set value is reached and remains for a specified period. The packaging is visually inspected for continuous bubble emission to identify any leaks or weak points in the packaging material.
Benefits of Vacuum Leak Testers
- Accuracy and Sensitivity
Vacuum leak testers are designed to provide relatively accurate and sensitive leak detection. They can detect small leaks, ensuring that tiny imperfections are identified. This level of precision allows manufacturers to identify and rectify any potential issues before they become major problems, maintain the highest quality standards, and meet regulatory requirements.
- Efficiency and Speed
With advancements in technology, vacuum leak testers have become more efficient and faster than ever before. Automated systems can test multiple packages simultaneously, significantly reducing testing time. This increased efficiency enables manufacturers to streamline their production processes and meet demanding deadlines.
- Non-Destructive Testing
One of the key advantages of vacuum leak testing is its non-destructive nature. Unlike other testing methods that may damage or alter the packaging, vacuum leak testers can detect leaks without compromising the integrity of the product. This is particularly beneficial for sensitive or fragile items that require intact packaging.
- Versatility
Vacuum leak testers are adaptable to various packaging types, including flexible bags, cans, bottles, pouches, and blister packs. This versatility makes them suitable for a wide range of industries, allowing businesses to conduct leak testing on different packaging formats.
What Factors to Consider When Choosing a Vacuum Leak Tester?
There are three factors below you have to consider when selecting a vacuum leak tester.
- Vessel Size
The transparent vessel, as the indispensable part of a vacuum leak tester, accommodates the samples you intend to test. The vessel shape generally includes cylinders or cubes. The vessel size is directly dependent on the greatest dimensions of your sample. Before making a purchase decision, you have to measure the size of the largest sample and ensure that the sample fits easily into the vessel and the container is deep enough to allow the sample to be completely submerged in fluid during the test.
- Vacuum level
The vacuum level is an essential indicator of a vacuum leak tester, which directly determines the performance of the machine. A higher vacuum level means that the equipment has the ability to subject the sample to higher negative pressure and accept more severe test conditions during testing.
For general, flexible packaging airtightness testing, a machine with an ultimate negative pressure of -100 kPa can meet all testing requirements according to ASTM D 3078. When you buy a vacuum leak tester, you must clearly know the anticipated test vacuum level you want and then choose a machine with a test capacity that is slightly higher than the target value.
- Ease of Use
Whether the machine is easy to use is also a point that you need to focus on. If the operation process of a vacuum leak tester is too complicated or the machine function is too simple, it will not be conducive to efficient and enjoyable experiments.
During the test, you are required to observe with your eyes whether there are continuous air bubbles generated from possible leaks on the surface of the sample. If the operation process is too cumbersome, different areas need to be set up during the test, manual timing is required, etc., these factors will interfere and distract you from making subtle observations.
Where to Buy the Vacuum Leak Tester for Packaging?
If you are confused about where to get an appropriate vacuum leak tester for packaging, AmadeTech is a supplier that you can trust. AmadeTech is a professional sealing testing equipment provider. We can provide you with the best solution for all your airtightness testing needs.
One of the key aspects that sets us apart is our commitment to offering flexible product sizes. We understand that packaging requirements vary across industries, and that’s why our Vacuum Leak Tester is available in a range of sizes to accommodate diverse packaging dimensions. Whether you have small, medium, or large packaging, we have the perfect solution to meet your specific needs.
Besides flexible product sizes, we also offer rich configurations for our vacuum leak testers. We believe in providing our customers with options that suit their unique requirements. For example, the control panel consists of traditional key panel and touch screen panel. Our testers can be customized with various features and specifications, ensuring that you get the most efficient and effective solution for your packaging quality control. In addition to providing airtight testing equipment for flexible packaging, we can also provide instruments specially used for testing the airtightness of containers such as plastic bottles and iron cans.
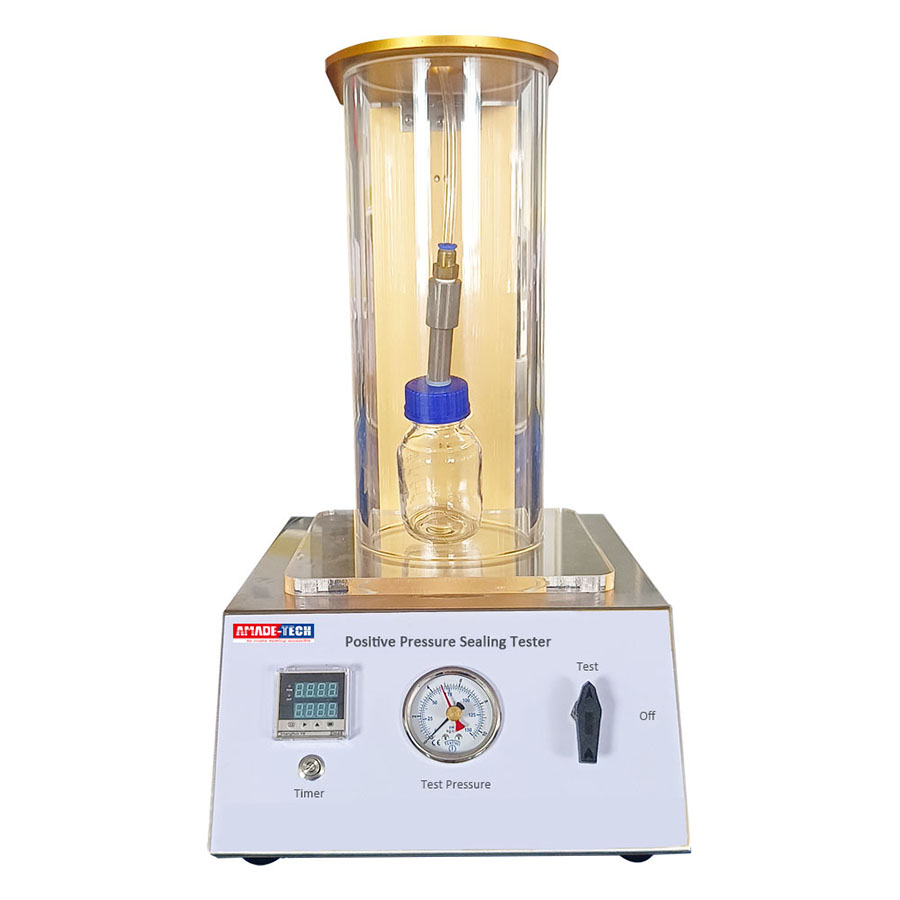
Positive Pressure Sealing Tester for bottles
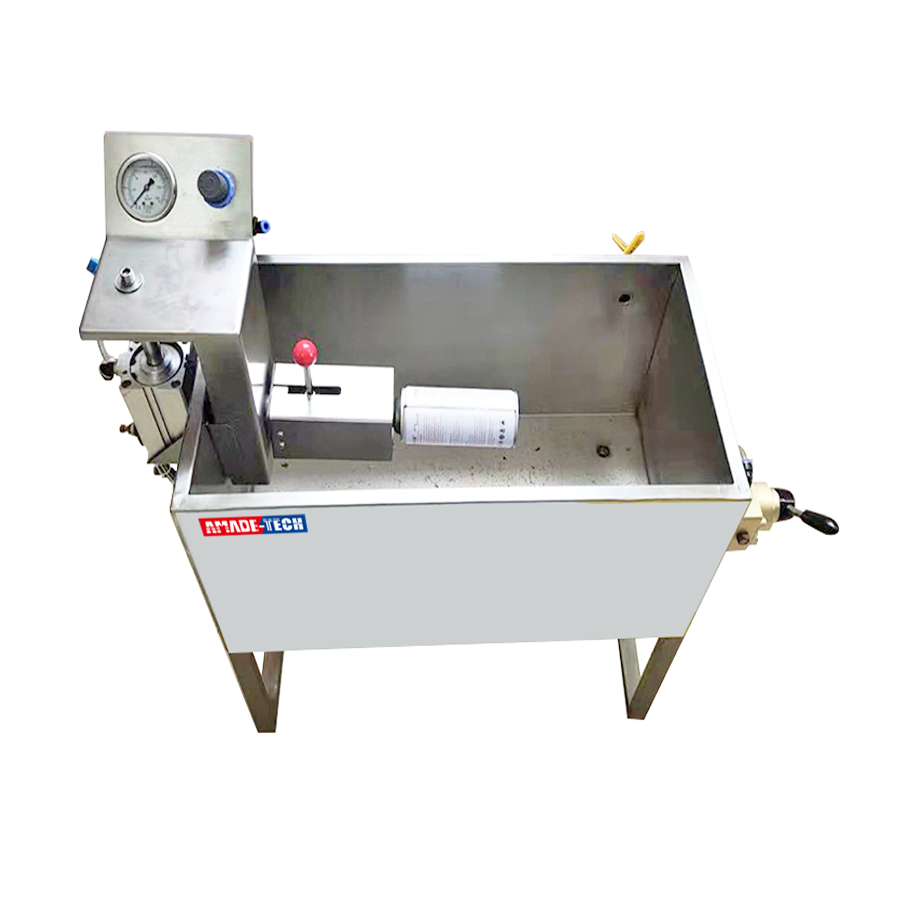
Sealing Test Machine for tin cans
When it comes to pricing, we take pride in offering a competitive edge. We understand the importance of delivering value to our customers, and we strive to provide top-quality products at a reasonable price. With our Vacuum Leak Tester, you can be confident that you are investing in a cost-effective solution without compromising on performance or reliability.
What’s the Advantage of the Vacuum Leak Tester from AmadeTech Over Others?
The Vacuum Leak Tester from AmadeTech offers several distinct advantages over other products in the market:
One-key Automatic Run
Our vacuum leak tester simplifies the testing process by providing a one-key automatic run feature. This means there is no need for extra operations during testing, which enables you to focus on observation for bubble emission.
Vacuum Controller from Panasonic
To ensure precision and reliability, our leak tester is equipped with a vacuum controller from Panasonic. Panasonic is renowned for its high-quality and accurate control systems, guaranteeing accurate results every time.
Unique Slotted Sealing Ring
We have designed a unique slotted sealing ring for the sealing barrel of our leak tester. This innovative feature ensures excellent airtightness, eliminating any leaks or inconsistencies in the testing process. With our leak tester, you can trust that the results are reliable and of the highest quality.
Maintenance-Free Vacuum Pump Adopted
Our vacuum leak tester is equipped with a maintenance-free vacuum pump. This means you don’t have to worry about regular maintenance or the hassle of adding oil. The pump is designed to be durable and reliable, providing consistent performance over a long period.
Two Different Air Sources Available
Depending on your specific requirements, our leak tester offers two different air sources. You can choose between using a built-in vacuum pump or an external air compressor. This versatility ensures that our leak tester can adapt to different testing scenarios and provide optimal performance in any situation.
To purchase our vacuum leak tester for packaging, you can directly contact us at AmadeTech. We have a dedicated team of professionals who will guide you through the entire process, from understanding your requirements to selecting the right configuration for your specific needs. Our customer-centric approach ensures that you receive personalized assistance and support throughout your buying journey. Contact us today to take the first step towards enhancing your packaging integrity and ensuring customer satisfaction.
Conclusion
Vacuum leak testing is a critical process in the packaging industry, ensuring product quality, consumer safety, and cost reduction. The introduction of automatic vacuum leak testers has revolutionized the way manufacturers detect and prevent leaks in their packaging. With their accuracy, efficiency, non-destructive and versatility nature, these innovative machines offer numerous benefits and have become an indispensable tool for manufacturers worldwide. For more details, please feel free to reach AmadeTech to get your answers.