AMADE TECH is a professional manufacturer of lithium-ion battery safety testing equipment in China. We can provide customers with a complete set of test equipment in accordance with IEC61233-2.
The lithium-ion battery test equipment that complies with the IEC62133-2 standard is mainly used for the safety testing of cells or battery packs of portable devices. The lithium-ion cell/battery is tested for safety primarily to verify that it can withstand the foreseeable misuse in daily use or during transportation.
IEC 62133-2 lithium-ion battery test equipment includes battery charge-discharge cycling tester, explosion-proof test chamber, external short-circuit tester, free fall tester, thermal abuse test chamber, crushing tester, vibration test machine, shock tester, forced internal short-circuit tester, DC power supply, etc.
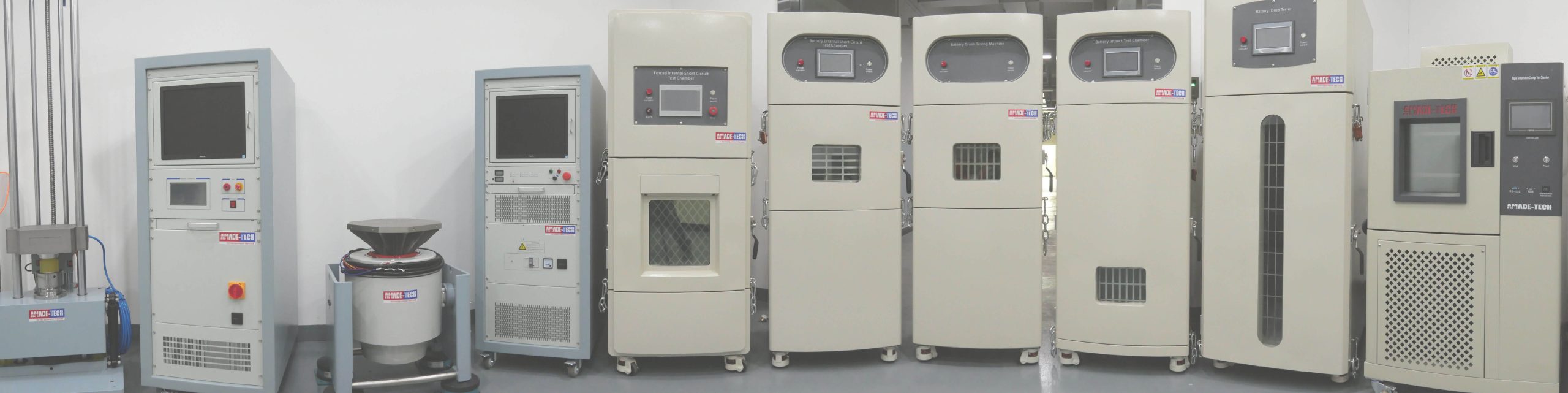
No. | Test Items | Required Equipment | Test Objects |
7.2.1 | Continuous charging at constant voltage |
| Cells |
7.2.2 | Case stress at high ambient temperature | High temperature test chamber | Batteries |
7.3.1 7.3.2 | External short-circuit |
| Cells & Batteries |
7.3.3 | Free fall | Free fall tester (Max. 3 kg load & Max. 1500 mm drop height / Max. 60 kg load) | Cells & Batteries |
7.3.4 | Thermal abuse | High temperature test chamber of Max. 200 degrees celsius (Explosion-proof) | Cells |
7.3.5 | Crush |
| Cells |
7.3.6 | Over-charging |
| Batteries |
7.3.7 | Forced discharge | Cells | |
7.3.8.1 | Vibration | Electromagnetic vibration system (Max. 300 kgf or Max. 600 kgf) | Cells or batteries |
7.3.8.2 | Mechanical shock | Shock system (Max. load 10 kg or Max. load 30 kg) | Cells or batteries |
7.3.9 | Forced internal short circuit test | Forced internal short-circuit test chamber | Cells |
What is Battery Test Equipment for IEC 62133?
Lithium-ion Battery safety test equipment for IEC 62133 is specifically designed to aid in the completion of tests for the safe operation of portable sealed secondary nickel or lithium-ion cells and batteries containing non-acid electrolytes under intended use and reasonably foreseeable misuse.
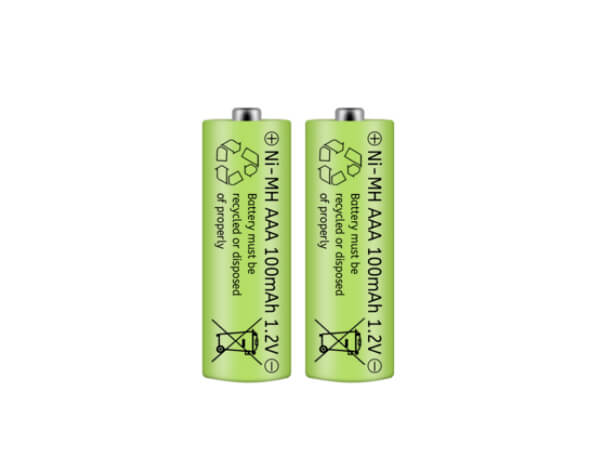
Ni-MH batteries

Ni-Cd batteries
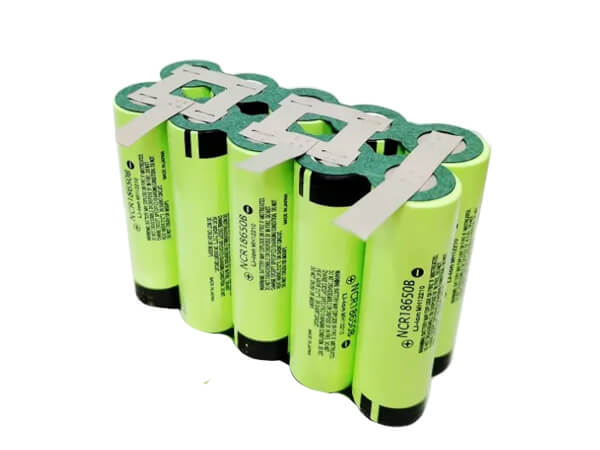
Li-ion battery module
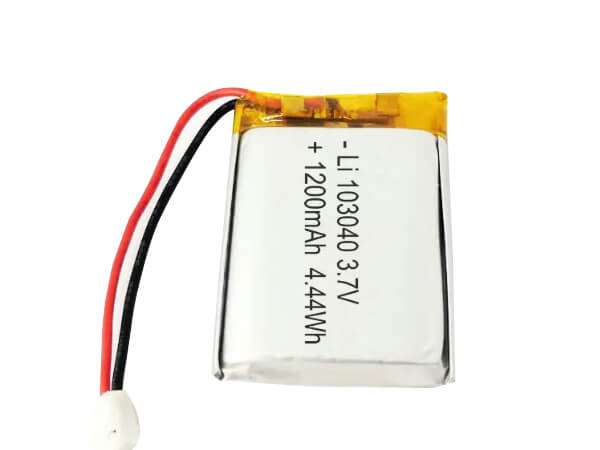
Polymer Li-ion battery
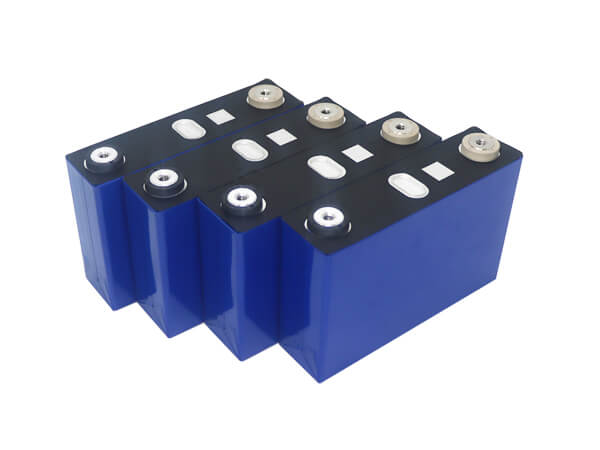
Aluminum-shell batteries
As we all know, the testing standards of IEC 62133-1-2017 and IEC 62133-2-2017 are published by the International Electrotechnical Commission, and they are important safety testing standards for nickel cells or batteries & Li-ion cells or batteries used in portable devices such as electric power tools, consumer electronics, beauty apparatuses, electric vehicles, etc.
According to the latest version of IEC62133, the safety test standards for nickel-based batteries and lithium-based batteries are separate. In the standard, the tests for nickel-based cells or batteries and lithium-based cells or batteries are only slightly different, but the same test items in the standard can share the same test equipment. Currently, most portable devices adopt lithium-ion batteries because of their small size, high energy density, and long service life. So in, most of the time, IEC 62133 test equipment we say refers to lithium-ion cell/battery safety testing equipment.
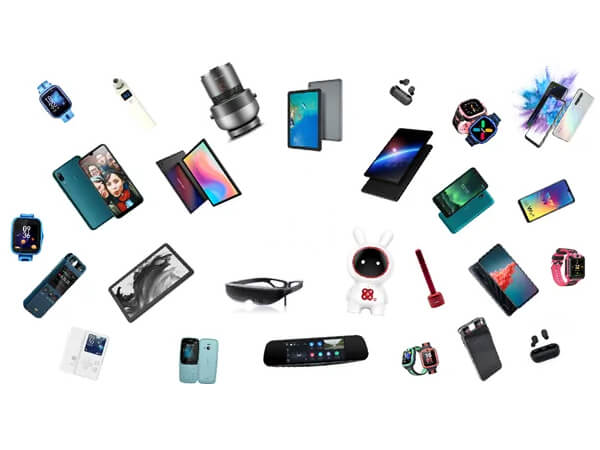
consumer electronics
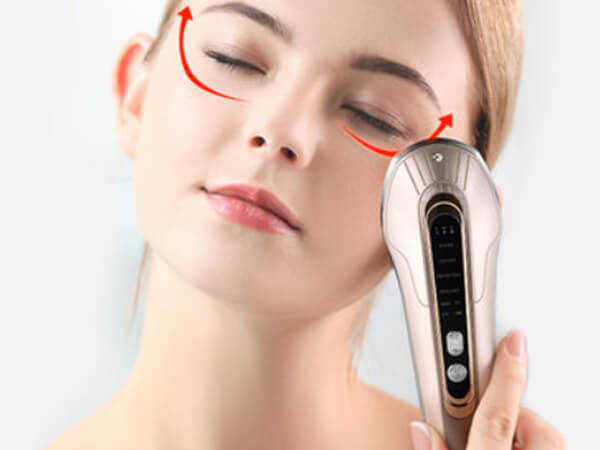
Beauty apparatus
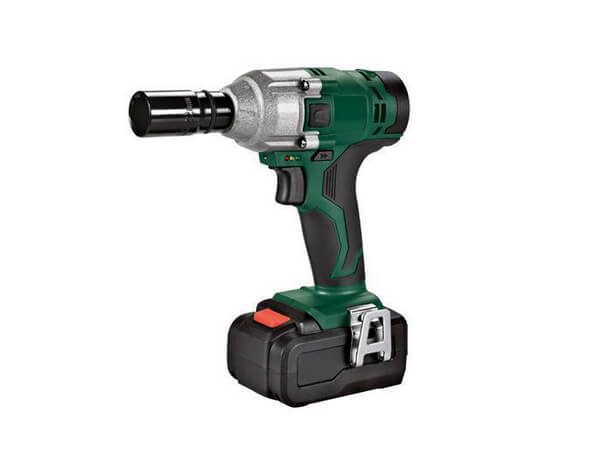
Electric power tool
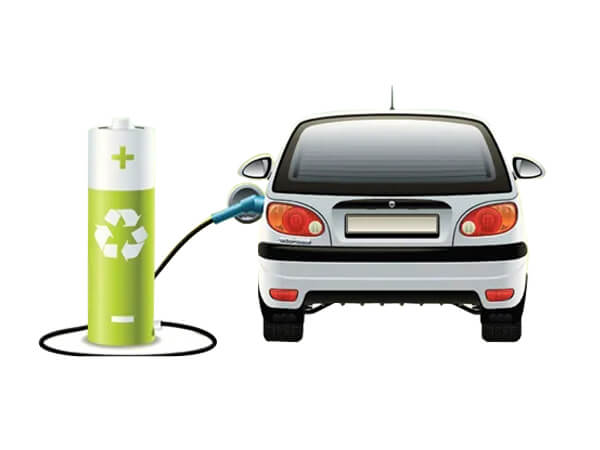
Electric vehicle
How to Use Lithium-ion Battery Test Equipment for IEC 62133-2 for Safety Certificate?
We will introduce the test procedures of 12 test items covered by the intended use and the reasonably foreseeable misuse.
Because most of the IEC62133-2 test items require the batteries or cells to be fully charged before the test, the standard lists 2 charging methods for test purposes as follows for you to observe:
7.1.1 First Procedure
Before charging, you have to discharge the battery at (20±5)℃ at a constant current of 0.2 It A down to a specified final voltage specified by the manufacturer.
- Charging method: According to the method declared by the manufacturer
- Temperature condition for charging: Ambient temperature of (20±5)℃
This charging process applies to subclauses except for that stipulated in 7.1.2
7.1.2 Second Procedure
First, you need to stabilize the sample cells at ambient temperature of highest test temperature and lowest test temperature specified by the manufacturer for 1 hour and 4 hour respectively, then charge the cells with the upper limit charging voltage and maximum charging current specified by the manufacturer, until the charging current is reduced to 0.05 It A, using a constant voltage charging method.
For the intended use, there are 2 test items of Continuous Charging Test at Constant Voltage for cells and Case Stress Test at High Ambient Temperature for batteries as below.
7.2.1 Continuous Charging at Constant Voltage (Cells)
Required Equipment:
Charge-discharge Cycling Tester
Test Steps:
- S1) Charge the specimen cell to a full state using the above 7.1.2 charging procedure.
- S2) Connect the cells to a charge-discharge cycling tester, arrange the wiring connections, then charge them for 7 consecutive days (168 hours) with the charging method for current and standard voltage specified by the manufacturer.
Evaluation Criteria:
The specimen is eligible if there is no fire, no explosion, and no leakage during the test.
7.2.2 Case Stress at High Ambient Temperature (Batteries)
Required Equipment:
Thermal Abuse Test Chamber
Test Steps:
- S1) Charge the sample battery (only applicable to those with a moulded case) to a full state using the above 7.1.1 charging procedure.
- S2) Place the battery in a thermal abuse test chamber with the air circulating function and remain for 7 hours. The temperature inside the chamber is kept at (70±2)℃ during the test.
- S3) Remove the battery from the chamber once the given time is reached and allow it to return to room temperature.
Evaluation Criteria:
The specimen is eligible if no physical distortion of the battery case leading to exposure of internal protective components and cells.
For the reasonably foreseeable misuse, there are 10 test items covering External Short-circuit Test for the cells, External Short-circuit Test for the Batteries, Free Fall Test for cells or batteries, Thermal Abuse Test for Cells, Crush Test for Cells, Over-charging Test for Batteries, Forced Discharge Test for Cells, Vibration Test for cells and Batteries, Mechanical Shock Test for cells and Batteries, Forced Internal Short-circuit Test for Cells.
7.3.1 External Short-circuit (Cells)
Required Equipment:
Short-circuit Test Machine
Test Steps:
- S1) Charge the sample cell to a full state using the above 7.1.2 charging procedure.
- S2) Store and stabilize it at an ambient temperature of (55±5)℃ for 1 hour to 4 hours.
- S3) Attach a K-type thermocouple to the surface of the sample with high-temperature insulation tape.
- S4) Connect the positive and negative terminals with a total external resistance of (80 ± 20) mohm to ensure that the cell is short-circuited.
- S5) Keep the test for 24 hours or until the specimen surface temperature declines by 20% of the maximum temperature rise, whichever is the sooner.
Evaluation Criteria:
The specimen is acceptable if there is no fire and no explosion.
7.3.2 External Short-circuit (Batteries)
Required Equipment:
Short-circuit Test Machine
Test Steps:
- S1) Charge the sample battery to a full state using the above 7.1.1 charging procedure.
- S2) Store it at an ambient temperature of (20±5)℃ and attach a K-type thermocouple to the case surface with high-temperature insulation tape.
- S3) Connect the positive and negative terminals with a total external resistance of (80 ± 20) mΩ to ensure that the battery is short-circuited.
- S4) Keep the test for 24 hours or until the case surface temperature declines by 20% of the maximum temperature rise, whichever is the sooner.
(In case of a dramatic decline in the short-circuit current, an additional one hour of the test after the current reaches a low and steady-state condition is required. It is typically applied when each cell voltage(series cells only) of the battery is below 0.8 V and decreases by less than 0.1 V in a 30-minute duration.
Evaluation Criteria:
The specimen is acceptable there is no fire and no explosion.
7.3.3 Free Fall (Batteries or cells)
Required Equipment:
Free Fall Drop Tester
Test Steps:
- S1) Charge the sample battery or cell to a full state using the above 7.1.1 charging procedure.
- S2) Mount the specimen into the drop testing machine to drop it 3 times from a height of 1.0 meters onto a flat concrete floor or metal floor at an ambient temperature of (20±5)℃. The impacts are in random orientations.
- S3) Leave it for at least 1 hour after the test.
- S4) Carry out a visual inspection of the specimen.
Evaluation Criteria:
The specimen is eligible if there is no fire and no explosion.
7.3.4 Thermal Abuse (Cells)
Required Equipment:
Thermal Abuse Test Chamber
Test Steps:
- S1) Charge the sample cell to a full state using the above 7.1.2 charging procedure.
- S2) Place it in the thermal abuse test chamber featuring circulating air convection, at an ambient temperature of (20±5)℃, for 1 hour.
- S3) Start the test and allow the test chamber temperature to rise at a rate of (5±2)℃ to a temperature of (130±2)℃. The testing time is 30 minutes.
Evaluation Criteria:
The specimen is eligible if there is no fire and no explosion.
7.3.5 Crush (Cells)
Required Equipment:
Crushing Test Machine
Test Steps:
- S1) Charge the sample cell to a full state using the above 7.1.2 charging procedure at the upper limit charging temperature.
- S2) Place it on the corresponding plate of the machine to achieve crushing action at an ambient temperature. The crushing force is continuously increased to a maximum of (13±0.78) kN.
- S3) The force is released automatically once either the maximum force has been applied or an abrupt voltage drop of 1/3 of the original voltage has been obtained, whichever is sooner.
Note 1: The lengthways axis of the cylindrical or prismatic cell is parallel with the flat plates of the crushing test machine during the test, and only the wide side of prismatic cells is to be tested.
Note 2: The force is applied on the flat surface of the coin cell during the test.
Evaluation Criteria:
The specimen is eligible if there is no fire and no explosion.
7.3.6 Over-charging of Battery
Required equipment:
- Explosion-proof Test Chamber
- Rated DC Power Supply or Charge-discharge cycle tester
Test Steps:
- S1) Attach a thermocouple to the surface of the sample battery(for batteries with a case, the temperature shall be measured on the base), then place it in the test chamber.
- S2) Discharge the battery at a constant current of 0.2 It A to a final discharge voltage specified by the manufacturer.
- S3) charge this battery at a constant current of 2 It A using one of the below voltages:
S3a) 1.4 times the upper limit charging voltage specified by the manufacturer(but not more than 6.0 V) for single cell / single cell block batteries. (Refer to Table A.1 in IEC 62133-2)
S3b) 1.2 times the upper limit charging voltage specified by the manufacturer per cell for series-connected multi-cell batteries. (Refer to Table A.1 in IEC 62133-2)
S3c) Sufficient to maintain a current of 2.0 It A throughout the test or until the supply voltage is reached. - S4) Continue the test until the temperature of the outer case reaches steady-state conditions of less than 10℃ change in a 30-min period or return to ambient.
Note: You conduct this test at an ambient temperature of (20±5)℃.
Evaluation Criteria:
The specimen is eligible if there is no fire and no explosion.
7.3.7 Forced Discharge (Cells)
Required equipment:
Explosion-proof Test Chamber and Programmable DC Electronic load
Test Steps:
- S1) Put the sample cell in the test chamber and discharge it to the lower limit discharge voltage specified by the manufacturer.
- S2) Apply a forced discharge at 1 It A to the discharged cell to the negative value of the upper limit charging voltage. The total duration is 90 minutes.
S2a) Reduce the current to ensure that the voltage is maintained at the negative value of the upper limit charging voltage for the rest of the time once the discharge voltage reaches the negative value of the upper limit charging voltage within 90 minutes.
S2b) Continue the test until the time of 90 minutes is reached if the discharge voltage does not reach the negative value of the upper limit charging voltage.
Evaluation Criteria:
The specimen is eligible if there is no fire and no explosion.
7.3.8.1 Vibration (Cells and Batteries)
Required Equipment:
Electrodynamic Vibration Test System
Test Steps:
- S1) Charge the sample battery to a full state using the above 7.1.1 charging procedure.
- S2) Fasten the battery to the platform of the machine without distortion.
- S3) Start the test enabling sinusoidal vibration based on Table 3 in IEC 62133-2, repeating 12 times for a total of approximately 3 hours for each of 3 mutually perpendicular mounting positions. (One of the directions is required to be normal to the terminal face.)
Evaluation Criteria:
The specimen is eligible if there is no fire, no explosion, no rupture, no leakage, or venting.
7.3.8.2 Mechanical Shock (Cells and Batteries)
Required Equipment:
Mechanical Shock Tester
Test Steps:
- S1) Charge the sample battery to a complete state using the above 7.1.1 charging procedure.
- S2) Mount the sample into the shock tester.
- S3) Shock the test battery in each direction of 3 mutually perpendicular mounting positions of the battery for a total of 18 shocks. (For each shock, refer to Table 4 in IEC 62133-2)
Evaluation Criteria:
The specimen is eligible if there is no fire, no explosion, no leakage, and no rupture and venting during the test.
7.3.9 Forced Internal Short-circuit (cells)
Required Equipment:
Forced Internal Short-circuit Tester
Test Steps:
- S1) Charge the sample at (20±5)℃ following the manufacturer’s recommendation.
- S2) Discharge the same sample at (20±5)℃ at a constant current of 0.2 It A, down to the final voltage specified by the manufacturer.
- S3) Store the sample for 1 hour to 4 hours at an ambient temperature as stipulated in Table 5 of IEC 62133-2.
- S4) Charge the sample at an ambient temperature (specified in Table 5 of IEC 62133-2) at the upper limit charging voltage at the constant current specified by the manufacturer. Continue charging at constant voltage until the charge current drops to 0.05 It A when the upper limit charging voltage is reached.
- S5) Put the aluminum bag with the winding core and nickel particle into the chamber( The chamber temperature is specified in Table 5) for (45±5) minutes. (Refer to Clause A.5, Figure A.6, and Figure A.9 of IEC 62133-2 for sample preparation details)
- S6) Take the winding core out of the sealed package and connect the terminals for voltage measurement and the thermocouple for temperature monitoring on the surface.
- S7) Position the winding core to make sure that the nickel particle is under the pressing jig.
- S8) Remove the insulating sheet and close the chamber door.
- S9) Confirm that winding core surface temperature is in line with Table 5 in IEC 62133-2, and then start the test.
- S10) The pressing jig is moved down at a speed of 0.1 mm/s, and the voltage is monitored. When a voltage drop is detected (Drops more than 50mV compared to the initial voltage), the descent will be stopped automatically, and the position will be maintained for 30 seconds, and then the pressure will be released automatically. The descent will be stopped immediately if the force of the press reaches 800 N for a cylindrical cell or 400 N for a prismatic cell prior to the 50mV voltage drop.
Evaluation Criteria:
The specimen is eligible if there is no fire. The operator needs to record the force when an internal short-circuit occurs if there was no fire.
All of the above is a test overview of IEC 62133-2. For more details on test procedures, please comply with provisions in standard IEC 62133-2-2017.
Although UN38.3 and IEC 62133-2 have different issuing organizations and testing purposes (UN38.3 is specially formulated by the United Nations for the transportation of dangerous goods. It mainly evaluates the safety problems that may occur during the transportation of cells and batteries and ensures transportation safety. IEC 62133-2 is a standard developed by the International Electrotechnical Commission for judging battery quality, performance, and safety), but they have 5 devices that can be shared. They are:
- Vibration tester
- Shock tester
- External short-circuit tester
- Crushing tester
- Explosion-proof test chamber
What Is the Material of Chambers of Your IEC62133-2 Battery Test Equipment?
The chambers of the test equipment from us are made of 304 stainless steel, which has a stronger strength to resist the blast wave generated by the explosion of cells or batteries compared with that made of ordinary iron plate.
The thickness of the stainless steel sheet ranges from 1 mm to 6 mm, depending on different devices and sizes. For example, comparing the two explosion-proof battery test boxes with an inner chamber volume of 1 cubic meter and an inner chamber volume of 0.125 cubic meters, the thickness of the stainless steel plate of the former is greater than that of the latter. Because a larger explosion-proof test box means that the sample to be tested is a battery with a larger volume or energy, it has higher requirements for the explosion-proof performance of the chamber.
Of course, we can also design and produce according to the thickness and size of the inner chamber specified by the customers. Please feel free to contact our sales engineers if you have any questions.
How to Make Sure I Can See the Samples in the IEC62133-2 Battery Test Equipment While Testing?
For all closed test chambers, we have configured a piece of tempered clear glass in the door. With the help of lighting equipment, it allow you to observe the sample changes during the test.
For some equipment, such as the explosion-proof test chamber, if you want to monitor the state of samples under test, we can also install a high-definition camera inside the chamber for you.
What Measures do You Take on IEC 62133-2 Battery Test Equipment to Prevent Hazards in Case of Explosion?
First of all, for the equipment for test items that have the possibility of explosion under test, we use a box-type structure with two layers inside and outside, which can play a buffering role when encountering explosion.
Secondly, we use 304 stainless steel plates and cold-rolled steel plates of various thicknesses to form the enclosure. These high-strength materials can effectively resist the shock wave generated by the explosion and protect the people and objects around the equipment.
Again, we especially use high-strength hinges and add explosion-proof chains for the door and frame. The chains can ensure that the door and the frame are always connected no matter what happens, equivalent to owning an extra insurance for the safety of the equipment.
Where to Buy Battery Test Equipment for IEC 62133-2?
Battery testing equipment is not a TV, refrigerator, or washing machine that you can buy anytime at your local mall. Many regions and even countries do not have dealers that sell battery testing equipment. Even if there is, sourcing locally may not be your best option, given the cost.
With the development of the Internet, more people choose to use the Internet to find suppliers worldwide. It is the trend of world economic development, but it is a double-edged sword because more choices also mean that you need more substantial screening capabilities.
IEC 62133-2 battery testing equipment is not one machine but 11 different machines, so when you are looking for a supplier, you need to look at and evaluate them from multiple angles.
AMADE TECH, a manufacturer of battery testing equipment from China, is a dependable partner for you.
AMADE TECH is a leading manufacturer and supplier of battery safety testing machines. They have rich R&D and manufacturing experience in battery testing equipment and are committed to providing customers around the globe with high-quality equipment at reasonable prices.
You can rely on this company for all your requirement for IEC62133-2 battery safety testing. From the selection of raw materials and components to optimizing the assembly process, AMADE TECH pays close attention to every detail to ensure the reliability and stability of the finished products. All battery testing equipment supplied by AMADE TECH fully complies with IEC, UN, UL ISO EN, and other standards. You tell their salesman what standard you follow, and they will send you the catalog and technical parameters of all the machines required under the test standard. In addition to standard models, their machines can be tailored to the needs of individuals.
AMADE TECH has excellent before-sale and after-sale service teams. They have proficient communication ability to serve every customer. For more details, please get in touch with AMADE TECH now.