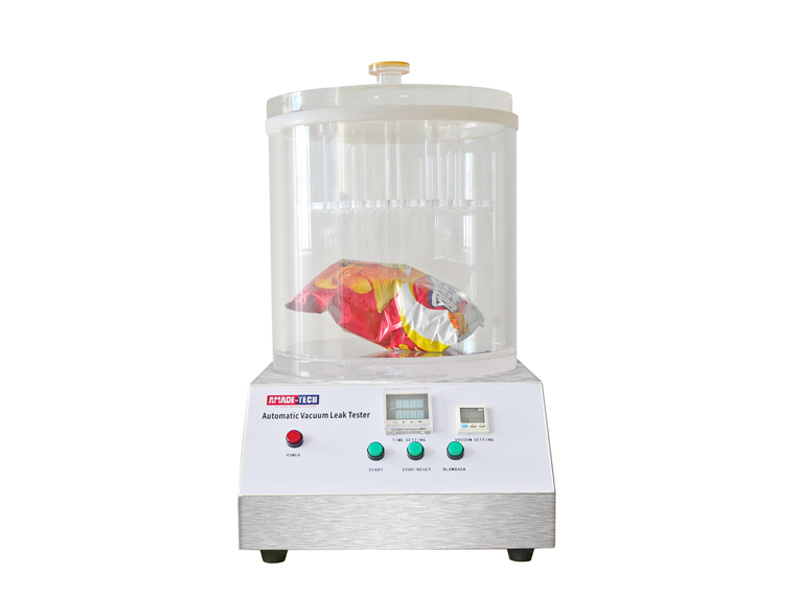
ASTM D3078 Vacuum Leak Tester for Flexible Packaging
Vacuum Seal Tester is an apparatus used to determine the airtightness performance of the packaging by detecting any leaks or defects in it. It is able to mimic the effects of atmospheric pressure changes on the packaging and effectively check the integrity and quality of the object under test. The entire testing process using this negative pressure leak tester is non-destructive to the sample.
The vacuum seal tester is primarily used in industries such as food, pharmaceuticals, electronics, and other sectors where the preservation and protection of products are crucial. It allows manufacturers to identify any potential defects or weaknesses in the packaging that could compromise the product’s quality or shelf life.
Vacuum Leak Test Principle
A sample is submerged in the fluid in the transparent container. A pressure differential is generated between the inside and outside of the sample enclosure after the container is evacuated to a specified vacuum level. The sealing performance is judged by visually observing the bubble emission. If bubbles appear continuously on the sample, it indicates that the sample has gas leaks.
Description on AmadeTech Vacuum Seal Tester
AmadeTech vacuum seal tester features a compact body and lightweight design. It consists of two parts: One part is a transparent cylindrical tank made of glass with enough strength to withstand test pressure as high as – 100 kPa, which is to create a vacuum environment. The tank has a lid with a handle, allowing it to be removed and returned conveniently. A transparent plastic accessory attached to the bottom of the lid enables completely pressing the sample into the water 25 mm from the water surface when in service. A grooved rubber sealing ring is provided to fit over the top edge of the tank, which plays a key role in excellent sealing between the tank and the lid. AmadeTech can offer tanks of different dimensions to fit samples of different sizes.
The other part is a unit incorporating control and power. A vacuum pump, processor, control valves, and other electronic components are built into it. We use a maintenance-free vacuum pump, so you don’t need to spend extra time and energy on refueling or other maintenance work throughout the life cycle. In addition, in order to ensure excellent reliability and durability, our machine adopts a complete set of pressure control systems from Panasonic, Japan.
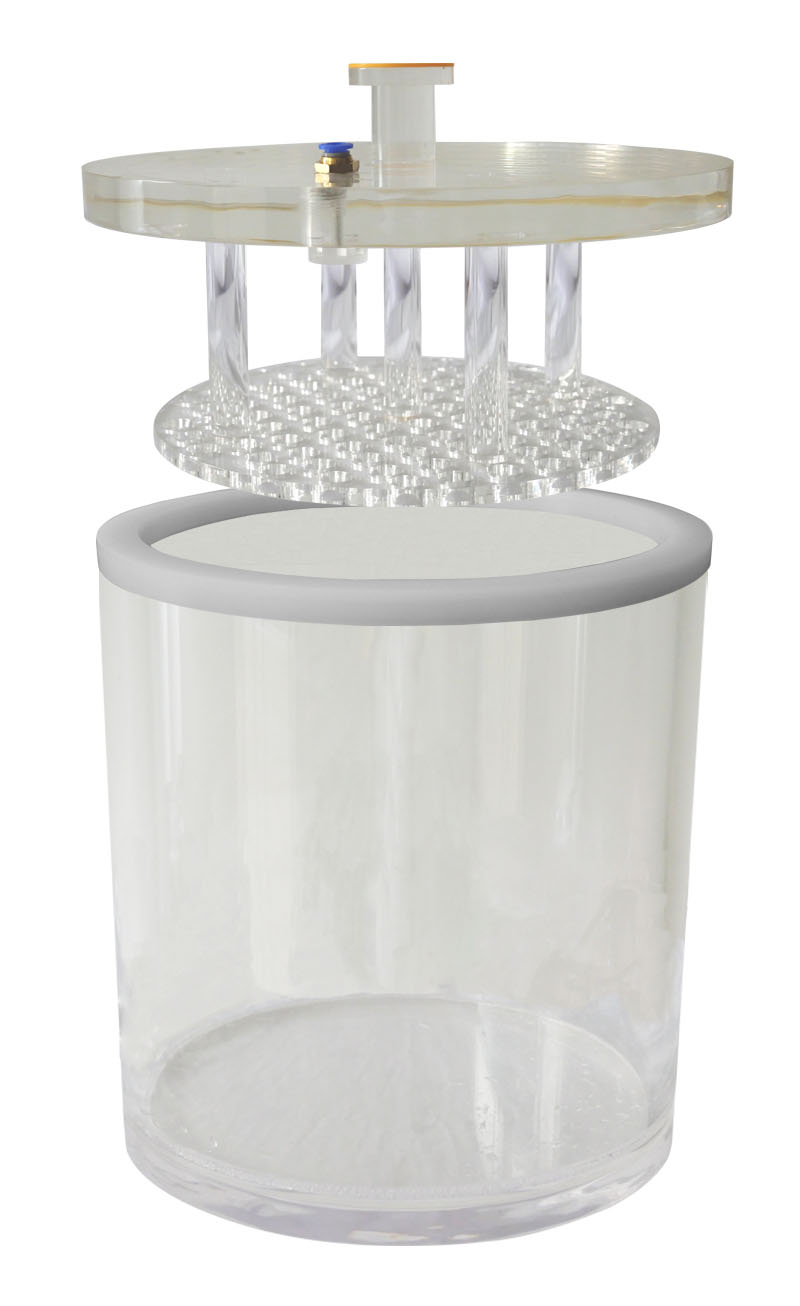
Transparent container
The traditional physical button operation panel or touch screen panel is available at AmadeTech to fit your taste. You are available to set an intended negative pressure and pressure holding time and start and stop the test through the corresponding keys or touch screen on the panel. The pressure remains for a required time once the preset value is reached. The whole test can be completed automatically, which won’t interfere with your observation of the bubbles. The controller is connected to the tank lid through a plastic tube.
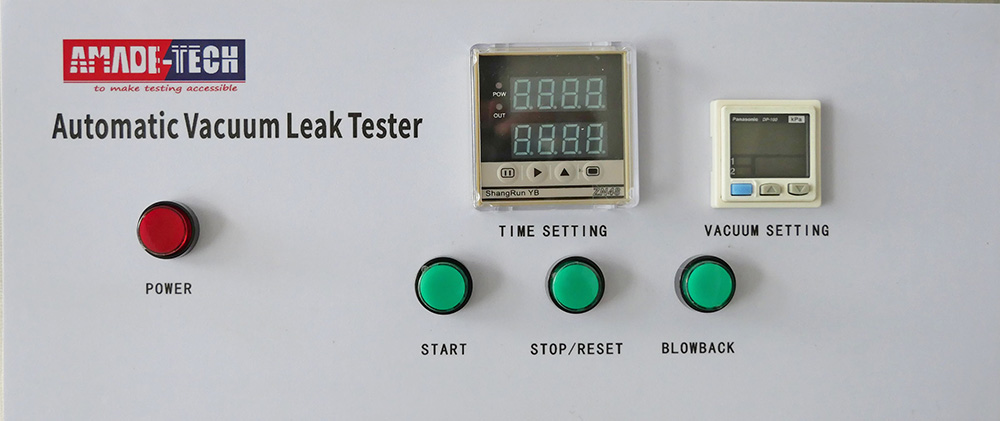
Physical button control panel
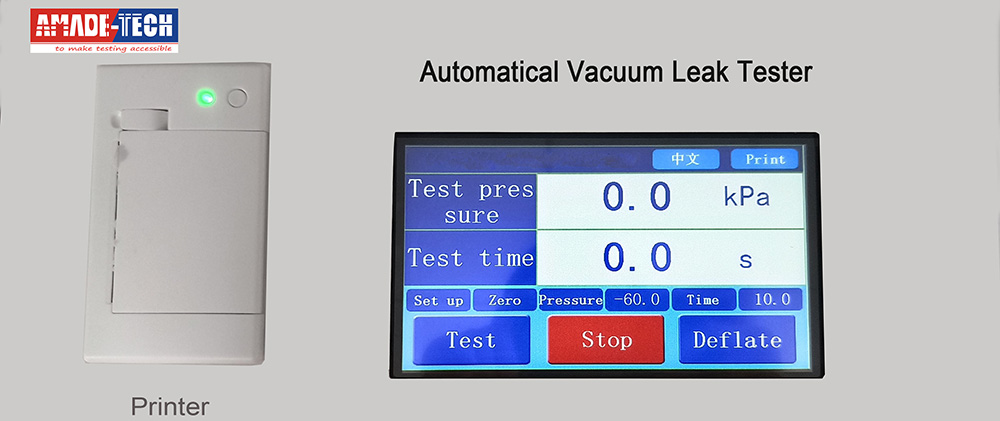
Touch screen control panel
Regarding the choice of air source, AmadeTech offers two options: Our default machine is a model with a built-in vacuum pump. If your laboratory has an air compressor, you can choose a model without a vacuum pump and use the air compressor as the air source. Please let us know if you have special needs before placing an order.
Model | AT-OA0003 |
Tank material | Organic glass |
Tank diameter | 300 mm (Optional) |
Tank height | 350 mm (Optional) |
Pumping rate | 90 L/m |
Vacuum range | Normal ~ – 100 kPa |
Display resolution | 0.1 kPa |
Measuring time | 5 ~ 9999 s adjustable |
Time accuracy | 1 s |
Air source options | Internal vacuum pump or External air compressor |
Noise | ≤ 55 db |
Vacuum pump power | 250 W |
Power supply | AC 220 V 50 Hz / AC 110 V 60 Hz |
Weight | Approx. 19 kg |
- ASTM D3078
- GB/T 15171
- The controller housing is made of stainless steel.
- A transparent barrel permits conveniently observing the sample for any bubbles.
- A variety of barrels of different sizes are available.
- Fitted with a durable and premium rubber sealing ring.
- Core parts are from famous Japanese and German brands to ensure exceptional reliability and accuracy.
- The microcomputer controls air extraction, pressure compensation, pressure maintenance, timing, pressure relief, etc., allowing automatic completion of the test.
- Equipped with LED displays to present the real-time pressure value and test time.
- Equipped with a button type or touch screen control panel.
- Two types of air sources for selection are available.
- User-friendly and easy to maintain.
Apart from the conventional models, AmadeTech also supplies high-end vacuum leak testers with bigger tanks or deeper simulation depth.
They feature three different test modes for you to select: Air pressure / Water pressure / Negative Pressure. Multiple locking bolts are equipped to guarantee airtightness between the lid and the container. The transparent tank enables you to observe the submerged sample suffering from the pressure for any harmful effects.
In addition to flexible packaging, these devices are used more for leak testing of mobile cellphones, underwater cameras, connectors, and other electronic products or as IPX8 waterproof testing equipment.
Positive or negative pressure and container volume for testing can be customized according to your sample size and test conditions.
Please share your requirements with us to get a matching solution now.
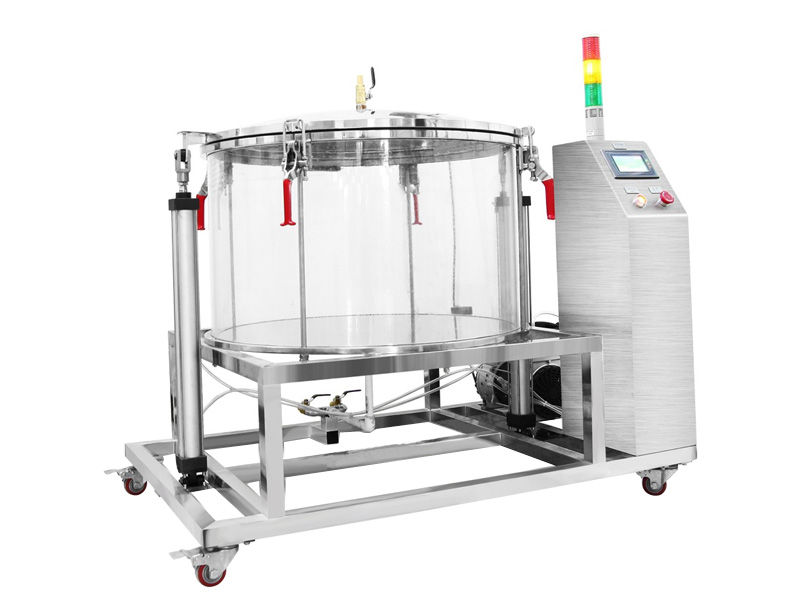
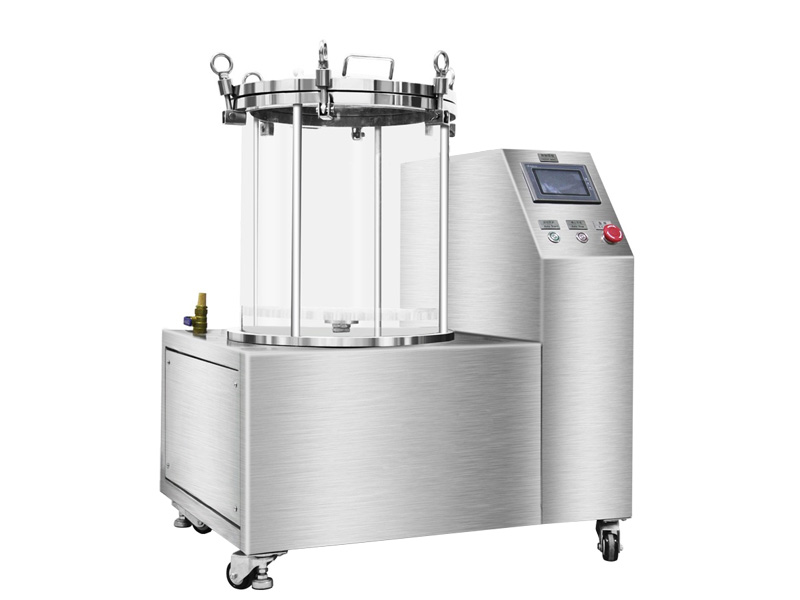
FAQs
Request a Quote Now
Please feel free to contact us for more details on the product, price, lead time, payment terms, shipment methods, etc. AmadeTech sales engineers will respond within one working day.